在表面貼裝技術(shù)(SMT)加工過程中,貼片元件被放置于印刷電路板(PCB)上并通過回流焊接來完成電路組裝。要實(shí)現(xiàn)高品質(zhì)、高效率的SMT加工,規(guī)范的PCB基板是關(guān)鍵。即使擁有最先進(jìn)的SMT技術(shù),如果PCB基板不符合標(biāo)準(zhǔn),也難以達(dá)到預(yù)期的效果。接下來SMT貼片加工廠家-宏力捷電子將為大家介紹實(shí)現(xiàn)高品質(zhì)、高效率SMT加工對PCB的要求。
一、適宜的PCB拼版尺寸
1. 尺寸要求:
- 拼版后的PCB尺寸在10-15厘米范圍較為適宜。太小的板子(小于5厘米*5厘米)貼片機(jī)難以處理,導(dǎo)致效率低下。
- 太大的板子(大于420*500毫米)超出了大多數(shù)貼片機(jī)的處理范圍,也會影響生產(chǎn)效率。
2. 板厚要求:
- 非必要情況下,不要使用過薄或過軟的板材。薄板和軟板在印刷定位和貼片支撐方面都存在挑戰(zhàn),通常需要制作專用治具,增加成本。
二、符合規(guī)范的Mark點(diǎn)和工藝邊
1. 工藝邊要求:
- 工藝邊寬度應(yīng)在5-8毫米之間,確保PCB在傳輸過程中穩(wěn)定。
- 工藝邊上應(yīng)合理放置Mark點(diǎn),以保證PCB在SMT設(shè)備上的精確定位和傳輸穩(wěn)定性。
2. Mark點(diǎn)要求:
- Mark點(diǎn)應(yīng)為實(shí)心圓,焊盤直徑1毫米,阻焊窗口直徑3毫米。
- Mark點(diǎn)表面應(yīng)潔凈、平整,顏色與背景有明顯區(qū)別,表面以沉金處理為佳,確保高對比度。
三、合理設(shè)計(jì)放置SMD元件
1. 元件分布:
- 高效率的SMT加工希望每個PCB上有盡可能多的SMD元件,減少進(jìn)出板和貼片頭空跑的時間浪費(fèi)。
- 避免單面只有少量貼片元件的情況,盡量將這些元件移至另一面,形成單面貼片板,提高效率。
2. 雙面貼片板設(shè)計(jì):
- 對回流溫度敏感的元件(如鏡頭和BGA)和自重較大的元件(如電感、卡座、連接器)應(yīng)放在同一面,只過一次回流焊。
- 另一面只放置電阻、電容、二三極管和普通IC,適應(yīng)兩次回流焊的要求。
四、優(yōu)選PCB表面處理
1. 沉金工藝:
- 對于0402及更小元件、精密BGA/QFN/QFP,建議采用沉金工藝,因?yàn)閲婂a工藝的平整性較差,影響錫膏印刷品質(zhì)。
2. OSP工藝注意事項(xiàng):
- 雙面貼片時,避免采用OSP工藝,因?yàn)樵谫N第一面時,第二面容易在高溫下氧化。
- 如果PCB需要長期庫存,避免使用OSP工藝,因?yàn)镺SP板在常溫下易氧化。
- OSP表面處理的PCB上有測試點(diǎn)時,要確保測試點(diǎn)上錫,因?yàn)楹附忧暗腛SP保護(hù)膜導(dǎo)電性差。
五、焊盤和定位孔設(shè)計(jì)考究
1. 焊盤設(shè)計(jì):
- 焊盤形狀和大小需合理,過大容易導(dǎo)致元件在回流焊時歪斜,過小則難以保證上錫量。
- 密腳IC和連接器的焊盤不要過粗或過細(xì),確保貼片和焊接質(zhì)量。
2. 定位孔設(shè)計(jì):
- 卡座、連接器的定位柱必須與PCB的定位孔匹配。定位孔過小會影響插入,過大會失去定位作用。
實(shí)現(xiàn)高品質(zhì)、高效率的SMT加工需要PCB設(shè)計(jì)和制造嚴(yán)格符合規(guī)范。從拼版尺寸、工藝邊和Mark點(diǎn)設(shè)計(jì),到元件合理分布和表面處理選擇,每一個細(xì)節(jié)都直接影響到最終產(chǎn)品的質(zhì)量和生產(chǎn)效率。通過遵循上述要求,設(shè)計(jì)者和制造商可以確保SMT加工過程順利進(jìn)行,生產(chǎn)出高質(zhì)量的PCBA產(chǎn)品。
深圳宏力捷推薦服務(wù):PCB設(shè)計(jì)打樣 | PCB抄板打樣 | PCB打樣&批量生產(chǎn) | PCBA代工代料
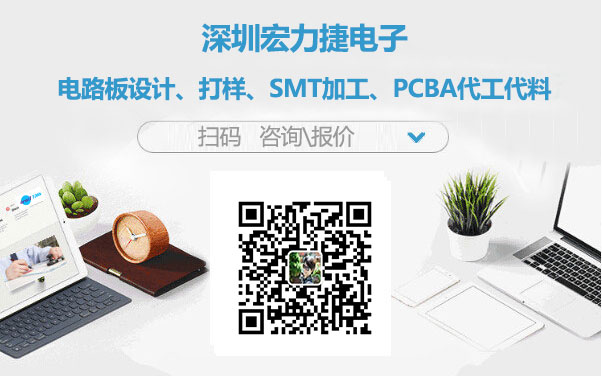