不知道怎么搞的,最近怎么有那么多人問深圳宏力捷關(guān)于
HotBar(熱壓熔錫焊接)的設(shè)計及生產(chǎn)問題,老實說自從有了
軟硬結(jié)合板(Rigid board)之后,深圳宏力捷個人就不太喜歡使用
HotBar(熱壓熔錫焊接)的設(shè)計了,因為HotBar(熱壓熔錫焊接)雖然可以省下1~2個連接器的費用并節(jié)省一些高度空間,但其生產(chǎn)的品質(zhì)問題也不少。
先看下面這個HotBar(熱壓熔錫焊接)設(shè)計的實際案例好了,這是一片單面的FPC,0.9mm焊墊寬度及0.9mm間隙的HotBar(熱壓熔錫焊接)焊墊設(shè)計,焊墊到焊墊之間的間距(pitch)為1.8mm,焊墊長度有5.0mm?;旧铣叽缫呀?jīng)夠大了,
PCBA工廠的吃錫也應(yīng)該不是什么太大的問題,可是偏偏生產(chǎn)時的不良率居然高達0.5~1.0%,而且絕大部分的不良都是短路。怎么會這樣?
就如同下面這張照片所顯示的,
PCBA工廠實際進行HotBar(熱壓熔錫焊接)焊接的時候,經(jīng)常會出現(xiàn)這類焊墊之間短路的問題,下面的圖示為比較嚴(yán)重的案例,大部分都只有部份溢錫,但這對品質(zhì)信賴度已經(jīng)產(chǎn)生了極大的危害,既使現(xiàn)在測試沒有出現(xiàn)問題,也難保日后在高溫高濕的環(huán)境下不會出現(xiàn)
電子遷移(Electromigration)的現(xiàn)象。
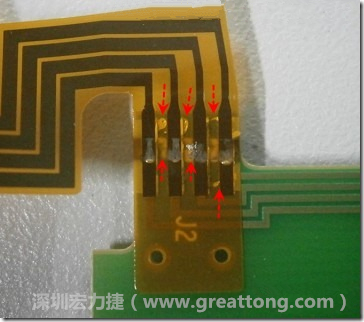
追究HotBar(熱壓熔錫焊接)溢錫的原因之前,深圳宏力捷想請看官們先想一下,為何HotBar(熱壓熔錫焊接)容易出現(xiàn)溢錫短路的問題?又該如何避免?
為何HotBar(熱壓熔錫焊接)容易出現(xiàn)溢錫造成短路?
這是因為HotBar(熱壓熔錫焊接)的熱壓頭(thermodes)下壓時,為了達到焊接FPC于PCB的目的,需要加熱并施以一定的壓力于事先印好錫膏并經(jīng)過回流焊(reflow)后的焊墊。
當(dāng)thermodes加熱時會重新熔融已經(jīng)吃在焊墊上的錫膏,熔融的錫又被來自熱壓頭壓力擠壓后,會順著可以吃錫的地方流動,如果吃錫的焊墊或FPC已經(jīng)滿溢無法再容納更多的錫,錫就會被迫往容易流動的地方宣洩,這時候最容易宣洩的地方就是焊墊與焊墊之間的空隙,而且上面還蓋有FPC,更容易形成所謂的虹吸現(xiàn)象(capillary action),造成短路的問題。
如何避免HotBar(熱壓熔錫焊接)發(fā)生溢錫短路問題?
既然知道了為何HotBar(熱壓熔錫焊接)容易出現(xiàn)溢錫造成短路?解決的方向有二,其一是減少多余的焊錫量;其二是增加可以容許焊錫外溢的空間。
下面這個HotBar(熱壓熔錫焊接)吃錫的設(shè)計已經(jīng)做對了一半,在印刷錫膏的時候在焊墊的中間位置減少錫膏,如果治具的設(shè)定正確的話,熱壓頭(thermodes)要壓在焊墊中間的位置,焊錫印出來結(jié)果如下面右圖所示。
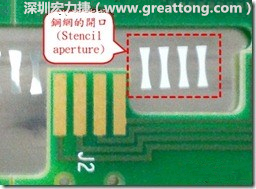
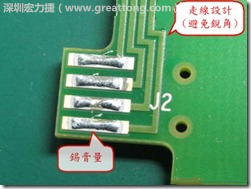
有沒有看到上面的問題點出在哪里?這個錫膏中間內(nèi)縮的距離還是不夠大,而且錫膏的厚度也太厚了,一般深圳宏力捷在設(shè)計HotBar(熱壓熔錫焊接)錫膏印刷于焊墊上的形狀時,像這種間距夠大的焊墊,深圳宏力捷通常將錫膏印刷成一長條狀于焊墊的正中間,錫膏只占焊墊面積的50%就可以了,這樣可以給予較大的空間給熱壓頭在焊墊的位置上下移動,而且也較能避免因為太多的焊錫而溢出焊墊。如果還是看不懂深圳宏力捷的敘述,有機會再來畫一張圖說明好了。
說完了第一種解決的方法,接著說明第二種解決方法-增加焊錫可以外溢的空間。這個方法通常要做設(shè)計變更,可以嘗試在FPC的金手指上下兩端打孔,讓擠壓出來焊錫透過通孔溢出。另外一個方向是把FPC上面的金手指設(shè)計得比PCB的焊點短。
以這個例子來說,深圳宏力捷會建議FPC上面的金手指焊墊長度從5.0mm減少到3.0mm,PCB的焊墊長度維持在5.0mm。HotBar(熱壓熔錫焊接)作業(yè)時將FPC的金手指對齊PCB焊墊的中間,兩端各留下1.0mm的空間,這樣可以讓多余的焊錫有更多的空間可以留在焊墊上而不會溢出來。
深圳宏力捷推薦服務(wù):PCB設(shè)計打樣 | PCB抄板打樣 | PCB打樣&批量生產(chǎn) | PCBA代工代料
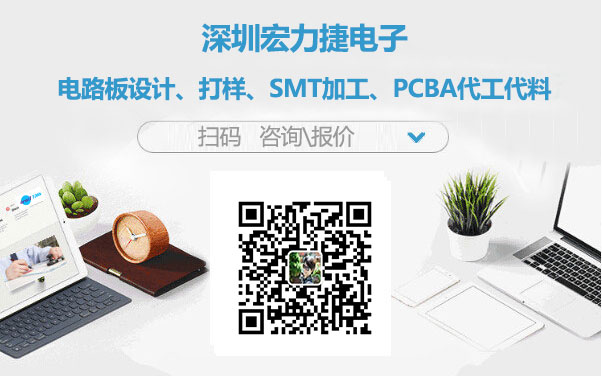